Overview of use and work procedures
Concrete cosmetic
Created by Synfola®
Overview of use and work procedures
for SBK-08 concrete cosmetic products
Reprofiling work with Rep-Mörtel (mortar)
Gravel pockets
Spallings
Indentations
Connection holes




Mixing with reprofiling mortar
Mix 1 kg Rep-Mörtel with approx. 230 to 280 grams mixing water M-10.
• For holes, gravel pockets or edges the surface needs to be cleaned, polished or the edges need to be rounded off.
• Paint (prime) the substrate with M-10 (mixing water
• Do not mix the Rep-Mörtel too thick for floor, stairway, façade, wall or masonry surfaces to assure that the substrate can still absorb liquid for the fixation.
2 to 3 minutes after the reprofiling work the reprofiled parts need to be levelled in order to receive a homogeneous optic. The elevations of reprofiled areas can also be cautiously pushed off after approx. one hour.
A: Cleaning and, B: priming reprofiling areas
C: Applying Rep-Mörtel
D: Levelling or pushing off




Manual structuring work with SSP (structure putty powder)
for floors, walls, ceilings and façades
Formwork panels in the wall surface
Planking with formwork joints



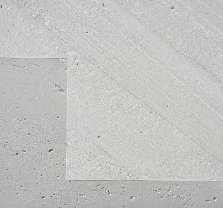
Stairway structuring
Floor structuring (elevator area)


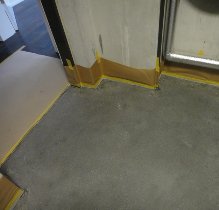
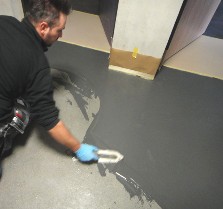
Structuring formwork on the ceiling
Floor structuring (school building)




Mixing with SSP (structure putty powder)
Mix 1 kg SSP (structure putty powder white) or the same total weight when blended with pigments or Be-dunkel and add 350 - 400 grams mixing water M-10.
Spread the desired concrete colour on the entire surface. Repair work before structuring shall always be conducted with the substrate colour.
• Always polish and prime holes, spallings, indentations or gravel pockets first, fill then with Rep-Mörtel and push-off with a blade before hardening.
• The prepared repair spots have to be primed with M-10 mixing water first. Then the spots have to be prestructured in the same colour with a structuring trowel or brush.
• Slightly polish the surface, suck it clean and prime once or twice depending on the absorbency. Then the surfaces can be structured with a structuring trowel in the desired concrete colour.
• Always build a quartz bonding bridge for outdoor wall capping sections before structuring. This prevents spalling due to frost damage.
• For façades, walls and ceilings the framework structures are only treated with a structuring brush and SSP and are subsequently slightly polished and impregnated.
Application of SSP and Be-dunkel concrete cosmetic products
with a low-pressure sprayer
Mixture for spraying
pigmented according to RAL or ca. NCS

Mixture for concrete cosmetic pigmented
• 1 bag of 500g pigments for 15.0 kg SSP In case of weak colour intensity the pigment amount can be increased. Attention - mix only up to max. 1.0 kg (2 bags) pigments for 15.0 kg SSP.
• For challenging colours (red, blue etc.) the pre-weight pigments should be soaked already the day before application with mixing water M-10 (weigh accurately), to assure that no pigment spots or strips occur.
Mixing with colour pigments: Mix 15 kg SSP (white) plus maximum 1.0 kg colour pigments according to RAL or ca. NCS plus 15 kg mixing water (M-10) well and repot it then.
Important: During repotting the coloured SSP needs to be sieved to assure that the spraying nozzle won't be blocked. The sprayer should use a nozzle no. 4 with 1.8mm nozzle diameter.
Application on concrete stairs and floors with yellow pigmentation



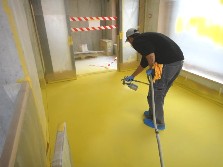
Hard concrete surfaces with colour pigmentation in terracotta



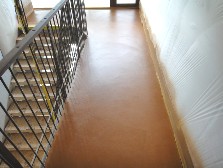
Later impregnation with Neutec LT 342 or Neutec LT 344

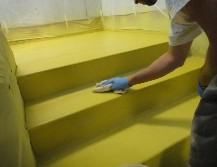


Application of Be-dunkel concrete cosmetic products
Mixture for spraying
Concrete grey (natural grey)
The mixing of the colour is done with SSP and Be-dunkel without additional pigments on the basis of prepared sample plates.
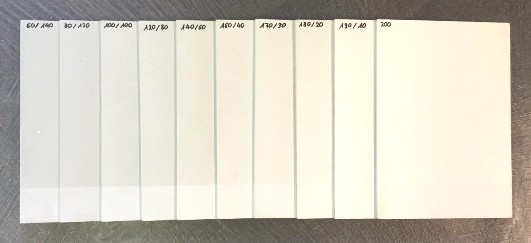
Mixture concrete cosmetic natural grey:
Mix SSP and Be-dunkel according to the colour sample plate.
For example: 180 parts SSP and 20 parts Be-dunkel.
• When mixing a concrete cosmetic product attention should be paid that the agitator (two disc stirrer) does not touch the bucket (risk of plastic parts in the mixture)!
• After mixing with M-10 (mixing water) the mixture should be repotted and sieved to assure that the spraying nozzle won't be blocked.
Application
Indoor
1. to 3. pass: Apply the concrete cosmetic with a low-pressure sprayer. The layer should be dried before applying the next coat. The drying process takes between 15 minutes and 3 hours depending on the weather condition and time of year.
4. pass: Shortly after the layer dried the area is slightly polished with a pad until the concrete has a fine surface. On the next day the concrete surface is hard and has to be polished with a fine sandpaper (180).
4.1 pass: (only outdoor) This step is conducted if rain is expected to prevent water stripes on the fresh concrete cosmetic. Apply a light impregnation on the ready processed concrete surface. Mixture: 1 part Neutec LT 344 with 5 parts water.
5. to 8. pass/impregnation: The impregnations are differently applied depending on the way of use.
Ceilings / walls / floors: 1. pass: mix Neutec LT 344 with 4 parts water.
Ceilings / walls / floors: 2. pass: mix Neutec LT 344 with 3 parts water
Walls / floors: 3. pass: mix Neutec LT 344 with 2 parts water.
Floors: 4. pass: mix Neutec LT 344 with 2 parts water.
Outdoor
All horizontal surfaces such as floors, wall cappings and windowsills are impregnated in the same way as described for indoor application (above for floor surfaces (floors)).
Facades and masonry
1. pass: mix Neutec LT 344 with 4 parts water.
2. pass: mix Neutec LT 344 with 3 parts water.
3. pass: apply Neutec LT 425 pure (without mixing).
Optical crack repair with SSP
The crack repair should only be applied on floors and walls that are at least 1 year old or only in urgent cases and on customer's own risk, as only after one year the present tensions in concrete are disappeared, that could cause cracks.
Mixture crack repair with structure mortar SSP: Mix 1 kg SSP structure mortar white and colour pigments or Be-dunkel and add 0.4 - 0.8 kg mixing water M-10.
The crack repair is always conducted slightly darker compared to the concrete substrate to make sure that the filled cracks are not lighter than the floor surface after drying.
• First the crack is filled with a mixture of 1 part SSP and 0.8 parts M-10, then it is slightly smoothed and pushed off.
• In the 2nd pass the crack is refilled with SSP as a mixture of 1 part SSP and 0.6 parts M-10, then slightly smoothed and pushed off again.
• Then the treated surfaces are polished and structured with concrete cosmetic in the colour of the respective surface with SSP / Be-dunkel. If required the treated surface can also be re-sprayed in a levelling way.
First processing step: Fill the crack with 1 part SSP / Be-dunkel and 0.8 parts M-10 (mixing water).




Second processing step: Refill the crack with 1 part SSP / Be-dunkel and 0.6 parts M-10 (mixing water), push off excessive material and slightly polish the surface.




Third processing step: Restructure the cracks with the floor colour, re-spray the structured spots in a levelling way with SSP / Be-dunkel and slightly polish, impregnate the floor surface afterwards.



